Digitalisierung der Werkzeugindustrie
Unter dem Thema „Vom Digitalen Zwilling zur Information Supply Chain“ versammelten sich auf Einladung der CIMSOURCE GmbH rund 40 Führungs- und Fachkräfte aus den Bereichen Werkzeugherstellung und –handel, Fertigung, Arbeitsvorbereitung und NC-Planung.
Dr. Götz Marczinski eröffnete die Veranstaltung mit seinem Vortrag über die Information Supply Chain. In der zerspanenden Industrie wird der Digitale Zwilling eines Werkzeugs lange vor seinem realen Pendant benötigt, er wird sogar zum Verkaufsargument: Wenn das digitale Produkt in der CAD/CAM-Simulation überzeugt, wird das reale Werkzeug gekauft. Probleme der digitalen Produkte sind die große Menge an unterschiedlichen Standards der Quell- und Zielsysteme, sowie die Notwendigkeit der wettbewerbsübergreifenden Zusammenarbeit.
Die „Anforderungen an die Datenbereitstellung“ waren das Thema der ersten Vorträge. Marco Merche von der Festo AG & Co KG in Esslingen stellte diese aus Sicht der Industrie vor. Bereits die Beschaffung der Werkzeugdaten, um die Datenbanken zu befüllen, sei problematisch. „Die Werkzeughersteller sind oft nicht in der Lage, alle gewünschten Informationen zur Verfügung zu stellen.“ Dies liege an den unterschiedlichen Standards und Qualitäten der Daten der verschiedenen Hersteller. Eine manuelle und damit sehr zeitaufwändige Erfassung der Daten sei die Konsequenz. Eine Einigung in Bezug auf die Standards und ein Kreislauf des ständigen Austausches könnten diese Problematik beheben. Die Metapher „Standards sind wie Zahnbürsten: Jeder hat eine, alle funktionieren ungefähr gleich, aber niemand möchte die des anderen benutzen.“ sollte sich als roter Faden durch die gesamte Veranstaltung ziehen.
Die CAM-Perspektive wurde von Michael Neubert von Siemens PLM repräsentiert. Zwar sei die Offenheit gegenüber anderen Systemen auch bei Siemens wichtiger Bestandteil der Unternehmensphilosophie, doch würden sie ihr Produktportfolio ständig so erweitern, dass sie in der „Digital Factory“ alles aus einer Hand anbieten könnten, um so eine funktionierende Information Supply Chain zu schaffen. In der Manufacturing Ressource Library könnten die benötigten Werkzeugdaten über „Vendor Catalogs“ importiert werden.
Einen Ausblick auf zukünftig steigende Anforderungen bot die Darstellung zur Entwicklung eines CAS (collision avoidance systems). Damit ist beabsichtigt, NC Programme auf der Maschinensteuerung vor dem realen Einsatz durch Simulation abzusichern. Um die dafür benötigten Daten zu erhalten, hat die Firma Module Works GmbH das „Job Setup“ entwickelt. „Für eine genaue Kollisionserkennung sind präzise 3D Modelle erforderlich“, so Dieter Ottmann. Er erkennt vier Stufen der Dateneingabe, von der manuellen Eingabe aller Parameter bis zur direkten Verbindung und Kommunikation zwischen Werkzeugmanagement und -bibliotheken mit CNC CAS. Erste Tests der Datenbereitstellung seitens eines Werkzeugherstellers haben stattgefunden. Angestrebt wird die Anbindung der Hersteller-übergreifenden ToolsUnited Datenbank.
Im nächsten Block ging es verstärkt um Lösungsansätze. Konstantinos Bountolas von der Walter AG sprach aus der Perspektive der Lieferanten. Sein Unternehmen nutzt einen sog. „SalesSupport“-Server der CIMSOURCE GmbH für die Aufgaben der Datenbereitstellung. Damit kann die Walter AG Daten in verschiedenen Formaten für TMS und CAD/CAM exportieren. Auch die automatisierte Erstellung von sog. BMECat für den elektronischen Einkauf in verschiedenen Sprachen wird dadurch ermöglicht. Die entsprechenden Services wurden in die Webseite bzw. in den Web-Shop der Walter AG eingebunden und somit dem breiten Kundenkreise zugänglich gemacht.
Boris Kaiser von der CIMSOURCE GmbH erklärte die Lösungen seines Unternehmens noch tiefergehend. „Die herstellerübergreifende Datenbank ToolsUnited bündelt und harmonisierten die unterschiedlichen Quellformate und übersetzt sie in das gewünschte Zielsystem.“ Mit dem Produkt ToolLink wird gar eine direkte Kommunikation zwischen End-User und Hersteller geschaffen. Diese wird insbesondere dann notwendig, wenn es um Sonderwerkzeuge geht. Durch das Zusammenspiel beider Produkte soll eine 100%ige Befüllung der Werkzeugdatenbanken ermöglicht werden.
Unter dem Thema „Von der Datenplattform zum Internet of Tools“ ging es in den letzten Teil der Vortragsreihe. Dr. Marczinski gab in seinem Vortrag einen Überblick über „Internet of Things“ (IoT) Plattformen. „Es geht um die intelligente Vernetzung von Objekten via Internet und die Analyse von Daten, die auf diese Weise eingesammelt werden.“ Zum Digitalen Zwilling eines Werkzeugs, der den Soll – Zustand eines (neuen) Werkzeugs beschreibt, kommen die Daten aus dem Betrieb des Werkzeugs, also der Ist Zustand, den er den „Digitalen Schatten“ nennt. Mit einer IoT Plattform werden der Digitale Zwilling und sein Schatten in Beziehung gesetzt.
Wie genau die Rückkopplung von realen Einsatzdaten zum „Digitalen Zwilling“ umgesetzt werden kann wird im Projekt „Cute Machining“ (Cutting edge machining intelligence cloud) erprobt. Bei diesem von Dominique Preis (CIMSOURCE GmbH) vorgestellten Projekt ist beabsichtigt, aus der Maschinensteuerung die Daten zu sammeln, die Rückschlüsse auf den tatsächlichen Einsatzfall ermöglichen. Um diese Daten dem realen Werkzeug zuordnen zu können, wird eine neuartige Identifikationstechnik entwickelt. Die Idee ist, über ToolsUnited einen „Schwarm“ Daten sammelnder Werkzeuge zu orchestrieren. Die so gesammelten Daten können dann mit modernen Analysemethoden untersucht werden. Besonderes Augenmerk liegt aber auf der Erkennung von „Mustern“, um eine „selbstlernende Wissensdatenbank“ zu schaffen.
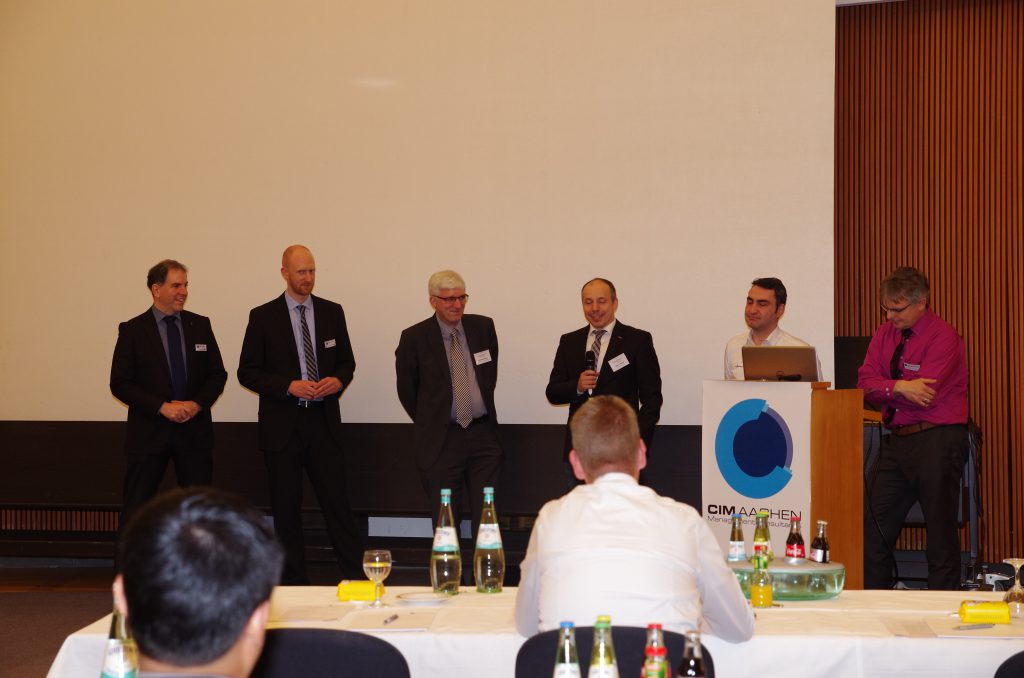
In der abschließenden Podiumsdiskussion wurden alle Referenten nochmals auf die Bühne gebeten, Dr. Marczinski moderierte. Einmal mehr wurden die unterschiedlichen Quell- und Zielformate zum Thema. „Bei den Kunden herrscht völliges Unverständnis für die vielen verschiedenen Standards“ so Dominique Preis. Boris Kaiser, selbst Mitglied der Gremien DIN4000 und ISO13399, weiß auch um die Unzulänglichkeiten der existierenden Standards. „Der Austausch von Schnittdaten wird immer wichtiger, die Möglichkeit existiert in den Standards aber noch gar nicht.“ Mike Neubert verwies auf die Fokussierung der „Big Player“ auf den an ISO13399 angelehnten GTC Standard. An dieser Stelle wurde die Qualität der Zahnbüstenmetapher nochmals sehr deutlich. Die abschließende Frage betraf das Consulting bei der Digitalen Transformation. Wer soll die Verantwortung übernehmen? Jemand Externes oder ein Mitarbeiter? Die Antwort war ein einstimmiges „Beide“. Einerseits sollte eine Consulting Firma wie die CIMAachen den Prozess begleiten, andererseits muss ein Mitarbeiter zum umsetzenden Ansprechpartner werden, der der Individualität von Unternehmen oder gar Abteilungen innerhalb des Unternehmens gerecht werden könne.
Zum Abschluss des Tages lud die CIMSOURCE GmbH alle Teilnehmer zu Speis‘ und Trank ins Barfüßer Brauhaus ein. Bei deftigem Essen wurde der Tag nochmals gemeinsam Revue passieren lassen und Beziehungen konnten aufgebaut oder vertieft werden.
David Westerbarkey – 05.02.2018